Lithium-ion batteries lose their juice over time, causing scientists and engineer to work hard to understand that process in detail. Now, scientists at the Department of Energy’s SLAC National Accelerator Laboratory have combined sophisticated machine learning algorithms with X-ray tomography data to produce a detailed picture of how one battery component, the cathode, degrades with use.
The new study, published May 8 in Nature Communications, focused on how to better visualize what’s going on in cathodes made of nickel-manganese-cobalt, or NMC.
In these cathodes, NMC particles are held together by a conductive carbon matrix, and researchers have speculated that one cause of performance decline could be particles breaking away from that matrix.
The team’s goal was to combine cutting-edge capabilities at SLAC’s Stanford Synchrotron Radiation Lightsource (SSRL) and the European Synchrotron Radiation Facility (ESRF) to develop a comprehensive picture of how NMC particles break apart and break away from the matrix and how that might contribute to performance losses.
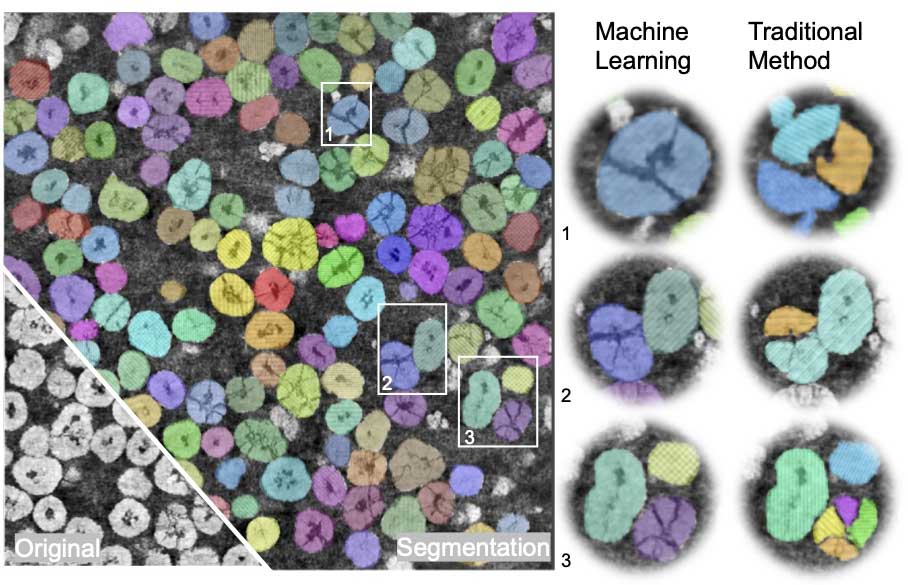
A new computer vision algorithm can better identify particles in an X-ray tomography image of a nickel-manganese-cobalt cathode. Older methods would mistake a single fractured particle for several different particles, while the new method can tell the difference. (Image courtesy Yijin Liu/SLAC National Accelerator Laboratory)
Of course, it’s a tall order for humans to figure out what’s going on just by looking at pictures of an NMC cathode, so the team turned to computer vision, a subfield of machine learning algorithms originally designed to scan images or videos and identify and track objects like dogs or cars.
Even then, there were challenges. Computer vision algorithms often zero in on boundaries defined by light or dark lines, so they’d have a hard time differentiating between several small NMC particles stuck together and a single large but partially fractured one; to most computer vision systems, those fractures would look like clean breaks.
To address that problem, the team used a type of algorithm set up to deal with hierarchical objects — for example, a jigsaw puzzle, which we would think of as a complete entity even though it’s made up of many individual pieces. With input and judgments from the researchers themselves, they trained this algorithm to distinguish different kinds of particles and thus develop a three-dimensional picture of how NMC particles, whether large or small, fractured or not, break away from the cathode.
They discovered that particles detaching from the carbon matrix really do contribute significantly to a battery’s decline, at least under conditions one would typically see in consumer electronics, such as smartphones.
Second, while large NMC particles are more likely to become damaged and break away, quite a few smaller particles break away, too, and overall, there’s more variation in the way small particles behave, said Yijin Liu, a staff scientist at SLAC and a senior author of the new paper. That’s important because researchers had generally assumed that by making battery particles smaller, they could make longer-lasting batteries — something the new study suggests might not be so straightforward, Liu said.
Original Article:
This article was originally published by the team at DOE/SLAC National Accelerator Laboratory.
Journal Reference:
Zhisen Jiang, Jizhou Li, Yang Yang, Linqin Mu, Chenxi Wei, Xiqian Yu, Piero Pianetta, Kejie Zhao, Peter Cloetens, Feng Lin, Yijin Liu. Machine-learning-revealed statistics of the particle-carbon/binder detachment in lithium-ion battery cathodes. Nature Communications, 2020; 11 (1) DOI: 10.1038/s41467-020-16233-5

HPQ Silicon is a Quebec-based TSX Venture Exchange Tier 1 Industrial Issuer. With the support of world-class technology partners PyroGenesis Canada and NOVACIUM SAS, the company is developing new green processes crucial to make the critical materials needed to reach net zero emissions.