It’s generally agreed that a robust solar industry is a key element in the quest to achieve a low-carbon economy. Worldwide, solar production has been rising by some 30% per year for much of the past decade.
At this rate of growth, solar energy is expected to provide over 10% of the world’s electrical power by 2030 and could be the world’s largest source of electricity by 2050.
Solar is often celebrated as a truly clean source of electricity, since in operation it has virtually zero impact on global warming.
Yet the manufacture and building of solar facilities still
From mining and manufacturing the components (think of racking, wires, panels, inverters) to delivery and construction, solar energy makes its small (but growing) contribution to the world’s carbon budget, a budget which – if the Paris goals are to be met – needs to be reduced by as much as 45% by 2030, and to reach net zero by 2050.
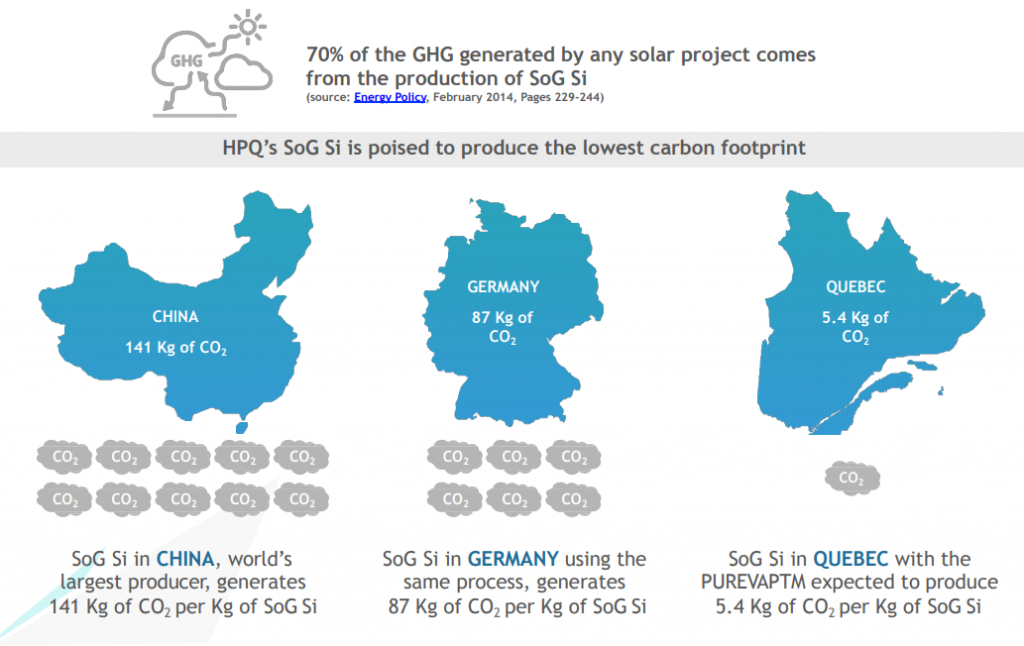
Within the process of creating solar energy plants, the production of the solar grade silicon (SoG-Si) used in the manufacture of cells and modules, which must be refined to a purity of 99.999% or better, is the most energy-intensive part of the process.
Research published in the journal Energy Policy (February 2014, pp. 229-244) found that roughly 70% of the greenhouse gas (GHG) emissions of solar energy production is generated through the manufacturing of SoG Si.
What this means in practice is that in China, for instance, where well over half of the world’s solar panels are currently produced, the manufacture of SoG Si generates around 141 kg of CO2 per kg of SoG Si.
In Germany, the same processes applied using less carbon-intensive electricity sources, generate only around 87 Kg of CO2 per kg of SoG Si.
The HPQ PUREVAP™ process can reduce these GHG emissions significantly, and by doing so totally disrupts the GHG impact of solar manufacturing.
By manufacturing SoG Si in Quebec, where electricity has a low carbon intensity, and using the efficient PUREVAP™ QRR Process, a new proprietary (patent pending) carbothermic process, we expect to generate a mere 5.4 Kg of CO2 per kg of SoG Si – a fraction of what other manufacturing processes are generating.
Indeed, this amounts to a potential carbon reduction for a project of 1100% below one that uses German-sourced SoG Si, and some 1800% less than one using Chinese sourced silicon.
With this level of carbon efficiency, the PUREVAP™ QRR process could help achieve significant reductions in the GHG impact of solar panel manufacturing worldwide.
The advances promised by the HPQ PUREVAP™ process could help to make solar power an even cleaner alternative to conventional fossil fuel power plants in terms of GHG emissions. As more and more solar plants are installed around the globe, this will make an increasing difference in ensuring that the carbon benefits of solar power make their maximum contribution to a more sustainable future.

HPQ Silicon is a Quebec-based TSX Venture Exchange Tier 1 Industrial Issuer. With the support of world-class technology partners PyroGenesis Canada and NOVACIUM SAS, the company is developing new green processes crucial to make the critical materials needed to reach net zero emissions.