The price of solar cells and modules has been falling steadily for decades, as technology and economies of scale, as well as the competitive environment, have all contributed to reduced costs through the supply chain.
The lower price of solar plants of course translates to a lower price for the electricity they generate, and has helped solar energy becoming increasingly competitive across a wider part of the globe.
The International Renewable Energy Association (IRENA) notes that solar has now become competitive with alternative or “traditional” sources of power in some 30 countries.
Recent auctions in developing countries have seen bids in the range of US$30 per MWh.
Manufacturers continue to focus on reducing costs, but as improvements continue, the opportunities to achieve price reductions are getting harder to achieve.
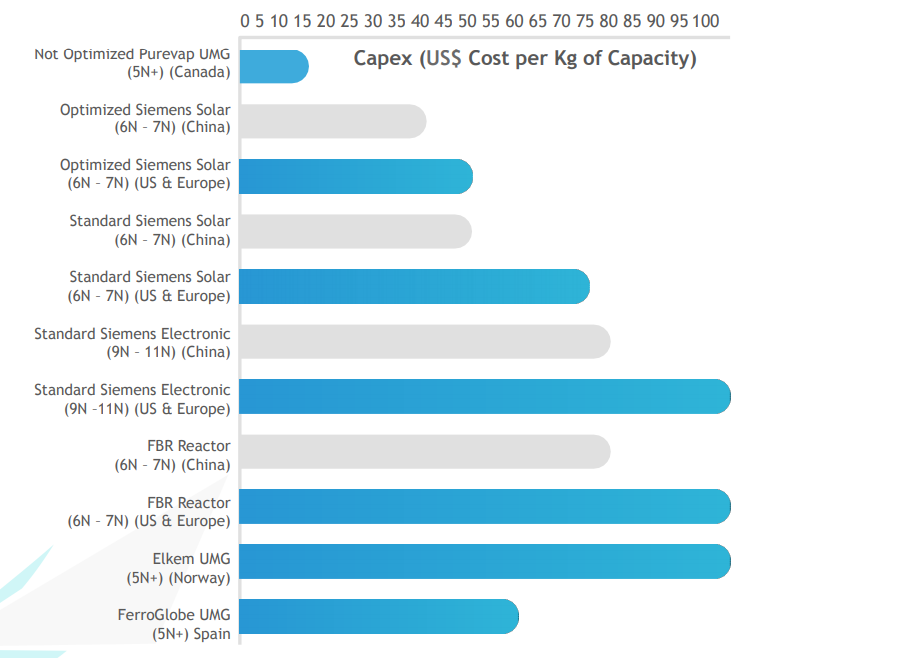
The benefits of economies of scale generally continue to favor the largest manufacturers, while the cost of key inputs like electricity and labor costs will give an advantage to those in developing economies, as they have in China, especially.
Also important, though, are the capital costs associated with the manufacturing process, which offer a unique opportunity to produce solar products at a lower cost.
An important stage at which cost improvements are being found is in the provision of Solar-grade Silicon (SOG-Si).
The PUREVAP™ UMG process can provide a significant dent in the cost of material inputs, in part by enabling a much lower CAPEX for the production of Upgraded metallurgical grade (UMG) silicon metal.
In fact, when compared to manufacturers elsewhere, the PUREVAP™ process is expected to provide the lowest CAPEX in the industry.
Consider low-cost panels from China. Where the SOG Si is manufactured under Optimized Siemens processes, the CAPEX typically comes in between $40 and $55 per kg of production capacity, while the Standard Siemens process – which is the most widely used globally – has a CAPEX of $50-75 per kg capacity.
Other processes include Siemens electronic ($80-100/kg), Fluidized Bed Reactors (RBR) ($80-100/kg). Other UMG processes have costs in the same range; Elkem in Norway came in around $100, though FerroGlobe’s plant in Spain has a CAPEX closer to $55/kg.
Innovation is expensive, but with the narrow margins of today’s solar market, keeping costs down is critical to competitiveness within the solar industry itself.
HPQ and its partners have invested in the PUREVAP™ process, and have found that the outfitting of a state-of-the-art commercial-scale manufacturing facility will require a CAPEX well below than that of its competitors, in the range of $15-20 at our intended site in Quebec. This is less than half the CAPEX of the next most competitive commercial process available.
It stands to reason that a company that can achieve 100% or better reductions in capital expenses will be at a considerable advantage in a market as competitive as today’s solar markets.
The improvements to SoG-Si manufacturing represented by the HPQ PUREVAP™ process can thus make a significant difference in competitiveness for the PV manufacturers and developers that will use it.

HPQ Silicon is a Quebec-based TSX Venture Exchange Tier 1 Industrial Issuer. With the support of world-class technology partners PyroGenesis Canada and NOVACIUM SAS, the company is developing new green processes crucial to make the critical materials needed to reach net zero emissions.